Here’s some great tips by Kalmario.
- Much has been said about thinning tops and bracing them. I would go a step further and say try to have the top and bottom sound boards vibrating differently (i.e either braced/not braced, or differently braced- use ladder on the bottom sound board as it takes less strain from the strings, or different woods/thicknesses) the sides make very little difference but need to be as stiff as possible! i.e. make them thick and solid!!
- The first thing I learnt from the old forum (pre nation days) was the sound hole size needs to be no bigger than a quarter. On a smaller box you can lose treble sounds with a sound hole too big.
- If you are going acoustic get the bridge in the middle of the sound board as much as possible, I forever see bridge near the tail of the guitar which will dampen the vibration and therefore the sound. Of course this can reduce the break angle that’s available, and it’s not important if you are planning on using it plugged in.
- The following is a photo of a bolt on neck design. Ignore the bent thread 🙂 but it gives another way of attaching a neck to a box. It has the advantage of being able to swap the box or neck out, and by changing the cut angle the neck can have a slight relief which makes it more playable – especially with fretted necks, you can get a really low action this way. Gives a lot of room inside the box for pickups too, as well as removing the weak point that normally happens with a stick through box design as the neck enters the box/ or the neck gets altered to make room for pick ups etc. Note the box has been re-inforced to handle the strain. And as you can see it can be forgiving for shoddy workmanship…
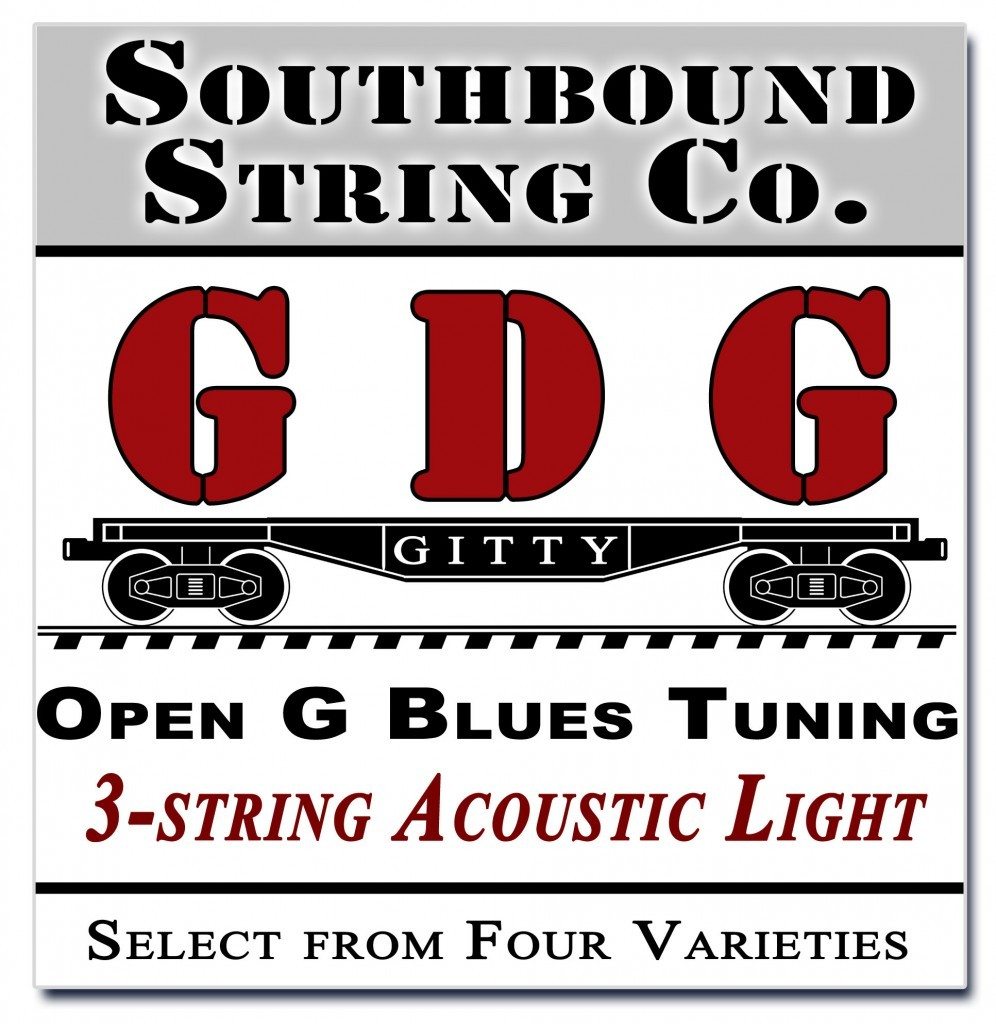